|
 |
In this series, I will not repeat the information that is already available on how superchargers work, but instead focus on their selection, installation, use and tuning on older motorcycle engines. Here I will make various observations and comments on function, and in some cases how to make improvements. New material will be added regularly, and eventually better organized. Click below to jump directly to an individual topic. |
Supercharger Topics | |
Function |
|
|
|
|
|
|
|
|
Carburetor and intake manifold modifications |
I make the assumption here that all prospective applications will use a carburetor, which may be placed either before (upstream of) the supercharger, as a “draw-through” system, or after (downstream of) the supercharger, as a “blow-through” system. Any supercharger will require considerable fabrication for either method. With the exception of some draw-through models that originally used an Amal or S.U. carburetor, all supercharger inlets will need some work, in some cases only a minor change in flange pattern, in others a complete re-location.
Blow-through
Here the carburetor remains at or near its original position between the intake manifold and the supercharger, and only pressurized air enters it from the supercharger’s discharge port. The carburetor’s position simplifies that part of the construction somewhat (throttle & choke linkage, fuel lines, &c.), but also poses some problems:
1. the carburetor must be sealed to prevent boost from escaping. Potential air leaks include the throttle
and choke shafts, air slides, air correction openings, float bowl vents, throttle cables, etc. The
leakage is harmless since it’ only air, but it will reduce boost and cause an irritating noise.
2. the float bowl must be pressurized as well.
3. the air cleaner must be re-located to the supercharger’s inlet port.
4. re-jetting is needed not only for the extra air, but because a carburetor cannot “see” and react
to a change in density (boost), but only to a change in velocity.
5. an intercooler between the supercharger and the engine will help suppress detonation and provide
more power in high boost applications.
6. the connection between the supercharger discharge and the intake manifold may be at any angle,
even straight up.
Blow-through carburetor selection should take into account how well sealed the throttle shaft and float bowl are, and how easy it is to apply supercharger discharge pressure to the float bowl vent.
The carburetor’s venturi (throat) size should be about the same as the original carburetor, and no larger than the largest factory high-performance carburetor. Since flow is already pressurized as it enters the venturi, a slight reduction in size does not reduce power significantly. If response is bad, use a smaller venturi (beginning with smaller primaries). A carburetor larger than needed frequently results in lean mixture that will not respond to normal jetting changes. A Keihin CV (“constant velocity”, the same principle as the S.U.) carburetor is available in different venturi sizes with the same basic body, so if response is bad, use a smaller venturi, if boost is limited (or mixture is too rich on top) use a larger venturi, etc. without complete new fabrication of cable, hoses, etc.
CV carburetors such as the S.U., Stromberg CD175, Keihin, Mikuni, &c. must have boost applied to both sides of the air valve or diaphragm.
A method of enriching mixture in closer proportion to rising boost pressure is to apply dynamic pressure (rather than static boost pressure) to the float bowl using a pitot tube, as explained: .
Carburetors with air correction jets must have boost pressure applied to the jet. Sizing should begin with the smallest number. For the Mikuni VM (part # BS30/97) this is the .5, or .50mm (.020”). In some cases a blank jet will produce better results. Carburetors with drilled passages such as Amal Monobloc and Concentric Mk I·, Linkert, S.U., &c. should explore drilling and tapping the passage for a common jet to make adjustments easier to perform and evaluate.
Common Mikuni jets, by size |
Part # | BS30/97 | 4/042 | N100.604 | N102.221 |
Thread | 4mm Χ .7mm | 5mm Χ .9mm | 5mm Χ .8mm (M5) |
Size | .5 - 2.0mm | 50-900 cc/min | 50 - 240 cc/min | 50 - 200 cc/min |
Blow-through jetting comments from Aerocharger for their product (slightly paraphrased):
“the modified HSR42T 42mm Mikuni turbo carburetor is calibrated specifically for the Aerocharger (for use on a Harley-Davidson 1340cc engine). A 32.5 pilot jet and 172.5 main jet are standard. Carburetors deliver the correct amount of fuel to the engine by sensing what is referred to as “pressure differential” between that float bowl and the venturi area inside the throat of the carburetor. The turbo carburetor has its float bowl vents pressurized by boost pressure. During operation on boost, the pressure in the high velocity venturi area is slightly lower that the float bowl area, and fuel is forced up the needle jet into the venturi. Because the float bowl area is pressurized, standard gravity fuel feed into the carb will not work. The turbo carb has a smaller 1.5mm needle and seat, and is kept full by a unique boost sensing fuel system. A high pressure constant flow fuel pump is utilized, which is regulated to about 30 psi by a bypass valve, which continually returns excess fuel to the tank via the vent line connected to the tank. A boost sensing final fuel regulator delivers fuel pressure to the carb at precisely 3.5 psi higher than boost pressure. For example, at 10 psi of boost, 13.5 psi of fuel pressure is required to ensure smooth fuel delivery.” |
Draw-through
Here the carburetor is mounted to the supercharger’s inlet port, and pressurized air/fuel mixture enters the engine’s intake manifold from the supercharger’s discharge port.
The carburetor is re-located to the supercharger’s inlet port. This is the easiest method in that the carburetor never “sees” boost pressure, and operates almost normally except for re-jetting. However, there are, again, some problems:
1. all the throttle and choke linkage, fuel hoses, air cleaner, &c. must mount very close to the
supercharger inlet.
2. a new manifold must be fabricated to adapt the supercharger discharge port to the engine’s
intake manifold on the head.
3. fuel vaporization produces some cooling and reduces the charge temperature below that of air, but
the entire tract between the carburetor and head (supercharger case, manifolds, etc.) now contains
a highly flammable gas mixture (rather than air as in a blow-through system), with a very serious
risk of explosion and fire should the engine back-fire, drop a valve, etc. Because of this, a
plenum or intercooler isn’t safe since it’s a potential bomb.
4. a draw-through installation must run downhill at a slight angle continuously from the carburetor to
prevent fuel from puddling in the supercharger or manifold.
5. jetting adjustments are still required, but cannot enable the carburetor to distinguish between
vacuum and boost.
6. Most available superchargers were designed for larger carburetors than the engine will use, which
restricts air volume entering the supercharger and reduces maximum boost, increases charge
temperature, etc. A carburetor large enough to match the supercharger’s inlet port simply does not
exist in some
cases, such as the Eaton; the throttle body on the General Motors M62 for the 3800 V6 is about
65mm or 2.56” diameter.
The optimum carburetor size is about what would support the same total power if normally aspirated, to reduce pumping loss. As a rough guess for size, use this formula:
CFM = Cubic centimeters Χ VE Χ RPM χ 56,633
then multiply by the pressure ratio:
Pressure ratio = (boost pressure + atmospheric pressure) χ atmospheric pressure
Example: a 750cc engine at 90% efficiency turning 7,000 RPM, with 10 psi boost and 14.7 psi local atmospheric pressure:
750 Χ .90 Χ 7,000 χ 56,633 = 83.4 CFM
(14.7 + 10) χ 14.7 = 1.68 pressure ratio
83.4 Χ 1.68 = 140 CFM
The exact CFM delivered by a carburetor is not a direct function of venturi or throat area, since internal streamlining affects this. In rough terms, the area of an excellent design (such as the Amal GP) multiplied by 133 is the CFM. The values shown below are based on this figure, and should be reduced for butterfly carburetors, carburetors with booster venturis, etc. - use a larger carburetor than indicated.
Venturi diameter vs. area vs. CFM |
Venturi ID |
Venturi area |
CFM |
Venturi ID |
Venturi area |
CFM |
20mm | .787” | .4865” | 65 | 32mm | 1.260” | 1.2469” | 166 |
22mm | .866” | .5890” | 78 | 34mm | 1.339” | 1.4082” | 187 |
24mm | .945” | .7014” | 93 | 36mm | 1.417” | 1.5770” | 210 |
25mm | .984” | .7605” | 101 | 38mm | 1.496” | 1.7577” | 118 |
25.4mm | 1.000” | .7854” | 104 | 40mm | 1.575” | 1.9483” | 127 |
26mm | 1.024” | .8236” | 110 | 42mm | 1.654” | 2.1486” | 136 |
27mm | 1.063” | .8875” | 118 | 44mm | 1.732” | 2.3561” | 146 |
28mm | 1.102” | .9538” | 127 | 45mm | 1.772” | 2.8055” | 166 |
29mm | 1.142” | 1.0243” | 136 | 46mm | 1.811” | 2.5759” | 187 |
30mm | 1.181” | 1.0954” | 146 | 48mm | 1.890” | 2.8055” | 210 |
As the carburetor size goes down, the pressure differential between the carburetor air-horn and the supercharger reduces boost, and increases charge temperature.
Comments frequently appear that state very strongly that “you must run a large carburetor to avoid engine damage”, “if the carburetor is too small it will run lean”, and “the minimum carburetor size needed for this application is XXX CFM, or YYY throttle area”. If considering an automotive carburetor, it almost certainly has a power valve (Holley), metering rod (Carter, Edelbrock, Rochester) or other vacuum-sensitive system to enrich the mixture under light throttle conditions. This is closed at idle and high vacuum conditions, and opens to admit extra fuel when vacuum drops to a pre-set level. A small carburetor will experience continuous vacuum at all throttle openings when positioned above the supercharger, and its vacuum-operated power system will never function. The power valve will remain closed, causing a dangerous lean condition which must be cured. This, and not the carburetor size, is what causes the lean condition. Attempting to cure this by increasing the jet sizes causes the engine to run full rich at all times. The cure suggested (large carburetors) reduces vacuum to the point where the power valve, metering rod, &c. is always open. This does cure the lean condition, but no longer provides accurate mixture for purposes other than full throttle.
With considerable testing, a power valve vacuum choice could be arrived at that will permit the valve to remain closed under the highest cruising speed and part-throttle acceleration the engine will see, but still open immediately upon throttle opening. This is an acceptable method, but there is no reliable way to tell in advance whether it will work or not. If the engine is too small (vs. carburetor size), vacuum will drop immediately upon throttle opening, and the range covered by a power valve may be too narrow to be acceptable for normal driving. |
A power valve carburetor can be modified to a boost-referenced power system. This references (controls) the power valve (or metering rod in Carter, Edelbrock, Rochester) to the engine rather than the supercharger. The concept is simple:
1. Find the small port in the carburetor base plate (facing the engine) that conducts vacuum internally
to the power valve or metering rod. It’s probably between the two primary throttle plates.
2. Plug the hole with a piece of lead shot or a set-screw at the gasket surface in the carburetor
baseplate, so that vacuum cannot enter this passage from the manifold.
3. Drill a hole horizontally in the side of the throttle body into the port above the plug.
4. Insert a tube or hose into this hole.
5. Connect the tube to a fitting in the intake manifold. This will provide vacuum to the power valve
normally, but permit the valve to open and enrich mixture when vacuum drops at open throttle.
Please note that motorcycle slide-type carburetors in general do not have power systems, and only a few throttle disc-type such as Mikuni BN, Tillotson, &c., and these comments to controlling the power system do not apply.
David Vizard suggests that a fabricated restrictor ring just inside the air-horn (but before the venturi and needle jet) will reduce pressure to the venturi, while air to the float bowl (from another source) is higher, causing automatic enrichment under boost. Different diameter restrictor rings will change the effect proportionate to their size, and may be used for pressure tuning. |
Air inlet size
The amount of boost pressure increases the minimum area of the air scoop or stack, but higher top speed decreases it (if pointing forward).
If the inlet area is too small, boost and power will be reduced, and pumping loss increased. If the area is too large air resistance is increased, and the scoop doesn’t function as efficiently.
The formula above determines the engine’s air requirement under boost, which is then used to calculate the smallest effective air inlet size. If the top speed is very high, the correct scoop size will be surprisingly small. Click here for an excellent on-line calculator:  |
Position
The supercharger’s position in relation to its drive mechanism must be sorted out before the remaining parts are fabricated. When this is established, the supercharger may “clocked” (rotated) around its drive axis to place its inlet or discharge ports in the most favorable position.
The nose length of the blower drive on the supercharger’ front end plate will determine the fore & aft or left to right position of the case on the engine. There are different length nose extensions available for the Eaton, Shorrock, Judson, and some others to position the pulley or sprocket at different distances from the front cover plate. The drive pulley on the supercharger end plate must line up with the pulley on the crankshaft, no matter what. Try to find a nose assembly and extension that will position your discharge pattern where you need it. |
Adapter Plate Dimensions
For a supercharger such as Eaton with a flat rectangular discharge surface, an adapter plate must be large enough to cover and seal the original discharge port, and should support all mounting points of the supercharger; this is much larger than the engine’s intake manifold.
The thickness of the adapter plate should be enough for beam strength so that it won’t ”bow” or flex under the tension of the drive system. Steel will work but will be very heavy. Aluminum 6061 would be my choice - it’s weldable, machinable, and easy to find. I'd try 1/2” thick; this need not be made of a single thickness, a “sandwich” of two thinner plates is just as effective and may be cheaper. |
Plenum
Engines equipped with positive displacement supercharger must use a plenum, or boost storage tank, between the supercharger discharge port and the engine’s intake valve. As a very general suggestion, the volume of the plenum, which also includes the volume of the entire tract between the rotor or vane and the intake valve, should be:
Plenum volume vs. engine type |
Type | % of one cylinder | % of full engine |
Single-cylinder | 200 - 250% |
Two-cylinder with 180° crankshaft (Honda, etc.) | 200 - 250% | 100 - 125% |
Two-cylinder with 360° (BSA, etc.) or V-twin crankshaft | 150 - 200% | 75 - 100% |
Three-cylinder | 100 - 150% | 33 - 50% |
Four-cylinder engines and centrifugal superchargers need less volume.
To calculate the plenum volume, first take the internal volume of the supercharger. For a twin rotor type positive displacement this is the supercharger capacity ÷ by the number of lobes on one rotor. E.g. an Eaton M62 is 62” capacity with three lobed rotors, so its internal volume for this purpose is 62 ÷ 3 = 20.7”.
For a twin screw-type positive displacement this is the supercharger capacity ÷ by the number of lobes on the male rotor. E.g. an Autorotor 1032 is 320cc or 19.5” capacity with a four-lobed male rotor, so its internal volume for this purpose is 19.5 ÷ 4 = 4.9”.
For a vane-type positive displacement use the capacity ÷ the number of vanes. E.g. a Shorrock C75 is 750cc or 45.8” capacity with four vanes, so its internal volume for this purpose is 45.8 ÷ 4 = 11.5” (source: Harry Pyle). |
Add to this figure the volume of any tubing &c. between the supercharger’s discharge port and the engine’s intake valve. A rough guess will suffice, here are some volume in cubic inches per running inch calculations for common tubing. |
Volume per running inch vs. tube ID |
Tube ID | Frac. in. | 7/8 | 15/16 | 1 | 1-1/16 | 1-1/8 | 1-3/16 | 1-1/4 | 1-5/16 | 1-3/8 | 1-7/16 | 1-1/2 | 1-9/16 |
Dec. in. | .88 | .94 | 1.00 | 1.06 | 1.13 | 1.19 | 1.25 | 1.31 | 1.38 | 1.44 | 1.50 | 1.56 |
MM | 22.2 | 23.8 | 25.4 | 27.0 | 28.6 | 30.2 | 31.8 | 33.3 | 34.9 | 36.5 | 38.1 | 41.3 |
Vol., in. of length | .60 | .69 | .79 | .89 | .99 | 1.00 | 1.23 | 1.35 | 1.48 | 1.62 | 1.77 | 1.92 |
|
See these Victory Library booklets |

|
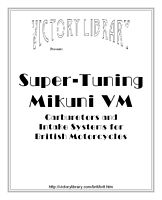
|
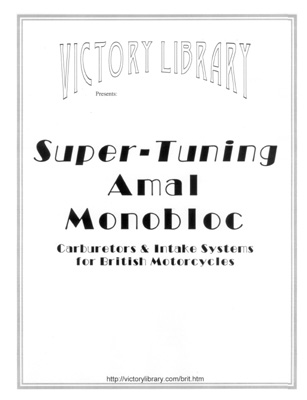
|
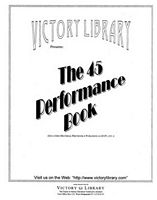
|
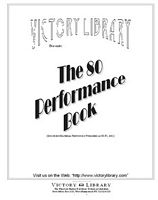
|
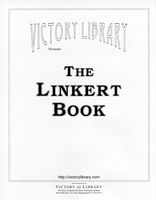
|
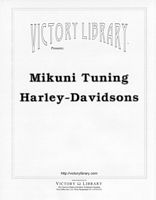
|
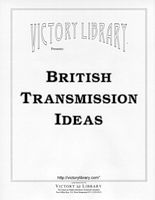
|
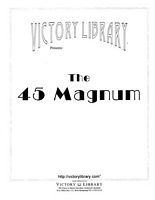
|
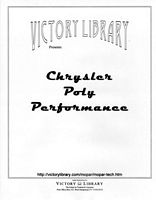
|
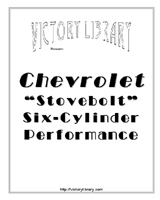
|
|